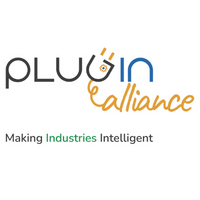
Plugin Alliance
View Brand PublisherCommunity Voices: How SwitchOn is enabling manufacturing companies reach zero-defects
SwitchOn helps precision manufacturing industries drastically reduce their manufacturing defects through the use of a one-of-a-kind field-trainable AI system.
Launched in 2017, SwitchOn eliminates defects in manufacturing by automating quality inspection through AI-powered vision inspection systems that supercharge quality assurance processes.
Aniruddha and Avra Banerjee had seen the automotive manufacturing industry very closely as a part of their earlier jobs, and had spent hours understanding the manufacturing environment. “While we saw that most of the manufacturing process itself was completely automated (with the use of Robots, Cobots, others,) the quality inspection was largely a manual process. This was slow, error-prone, and led to customer-recalls and product complaints on a regular basis. This is something we felt strongly about and wanted to automate,” Aniruddha explained.
While manufacturers had a bunch of convention quality inspection systems doing dimension check applications, surface inspection was still a very complex task. The systems setup for surface inspection needed 100+ images for each defect category, which customers would take over six months to configure and set up. This led to huge dissatisfaction and failure of most AI projects in the ecosystem.
The initial journey
The duo noticed that while AI and automation played a big role in the software industry, there was a lack of smart technologies like them in the manufacturing industry. It was this gap that led them to innovate in the Industry 4.0 space with SwitchOn.
SwitchOn helps precision manufacturing Industries drastically reduce their manufacturing defects through the use of a one-of-a-kind field-trainable AI system. Automotive and CPG companies globally employ 25 over percent of their workforce on inspecting product quality and yet face 500+ customer complaints per year per site leading to over $120 million in losses. The SwitchOn DeepInspect system can be trained by quality inspectors on the field to inspect complex surface defects and eliminate customer complaints through AI-on-the-Edge. Leading global manufacturers such as SKF, ITC, Unilever, and others are using the SwitchOn platform to give quality superpowers to their inspectors and ensure zero defects in their plants.
The SwitchOn difference
A major problem SwitchOn helped tackle is manufacturing defects in bottles. Over 72 percent of customers do not buy products due to this, and even refuse to associate their brand with bad experience.
They noticed that their customers were manufacturing bottles at a high speed of 350+ parts per minute so manual inspection of each bottle was not possible. In high speed lines even miniscule dirt inside empty bottles can lead to over 6 percent manufacturing defects, with the majority being shipped to the customer inside the box that cannot be seen. And in the world of high compliance risk in the supply chain, a defect in the labels or a change in the fill-level can cause up to 20 percent impact to manufacturer margins.
To that end, SwitchOn deployed their AI-powered SwitchOn DeepInspect System within three weeks to do a comprehensive inspection of their customers’ high-speed bottling lines. Customers can configure the hardware and software through one-click configuration software enabling them to flexibly inspect 10+ SKUs on the fly at 350+ parts per minute. Once configured, customers can use the AI-powered SwitchOn DeepInspect System to do comprehensive inspection of empty, filled, and labelled bottles through a single system.
They can visualise their line performance through integrated Industry 4.0 platform helping them root-cause manufacturing issues.
The impact
There were zero customer complaints in the products manufactured at the plant leading to improvement in wholesale margins, and there was over 80 percent reduction in cost of quality due to reduced manual inspection cost and regulatory compliant liability.
The path ahead
The founders say that they are rapidly expanding across the US and India, and are raising their Series-A round to fuel the growth. “We are seeing a rapid growth in adoption in both expansion across current customers as well as new customers in US and India,” Aniruddha added. Through the funding, they aim to set up teams in the US and India and support their customers better. “We are also looking to take our team from 24 to 60 in the next couple of quarters. In the long-term, our vision is to enable manufacturing companies reach zero-defects,” he signed off.
About Community Voices
Community Voices is a series of articles from the Innovent 4.0, an exclusive industry technology conclave from the Plugin Alliance — a first-of-its-kind Industry 4.0 alliance in India — with the aim to showcase India’s role in the Fourth Industrial Revolution. In tune with the event, the series will continue to highlight stories from Industry 4.0 startups.
that spotlights solutions and startups helping India’s manufacturing and supply chain industries benefit from smart technology. The series leads in to